亲临日本工厂之诸同仁所感
2010-10-18 0:00:00
在日方友人的推荐和周全安排下,借此次日本之旅,有幸参观了日本丰田集团和秋田工业,诸同仁在亲密接触了精益生产方式后,深有感触.以下略举一二.
小安:丰田工厂给人最深刻的印象,绝非是它那高度自动化和整齐、明亮、洁净的工厂,而是那寥寥无几的人.
小王:虽然此前在网上拜读过他人参观的感受,但是只有亲身实地参观过才知道什么是真正的震撼.令人震撼的不是其自动化的焊接机器人和先进的电子设备,而是一个团队的员工在高强度的重复性动作的工作状态下仍能不断的改善,值得让人学习和尊敬!我认为引进先进的设备和机器人并不难,难的是如何发挥员工的智慧来更好地利用这些设备.
小杜:……之后我们被带到车体焊接的混合生产线,隔着玻璃参观丰田的车间,这样就不会被焊接时发出的弧光所伤害.
感悟:丰田公司的安全防护措施做得很到位,它完全考虑了对到访者的安全保护,这一方面不仅向我们展示了一个公司对于安全的重视,更展现了丰田的人性化理念.于是我想到,我们在国内对客户企业作总体布局时值得借鉴这一理念.
小应:在丰田公司总能给你这样的一些感受.第一点:"这是一个高度遵守标准的团队",第二点是:"这是一个高效率、可信赖的公司".各种型号不同,颜色各异的车型可以在一条生产线上实现"0切换"、"平准化"生产,这应该就是精益生产所追求的"极致".相对于由3万多个零部件组成的汽车生产制造来说,要达到上述极致状态的唯一途径便是培养每一位能够严格遵守标准的作业员.包括从物料的搬运、传递,工序内品质保证,无疑都是由遵守作业标准的人来实现的.
小苏:在此对日本工厂的自动化程度就不作比较了.关于其他管理方面我有几点影响颇为深刻.
①小批量、多品种在一条线内同时生产:在一条线内出现几个型号的产品在同时生产.而我们大多使用专线或同一型号做足库存后再换成其他型号.
②专人进行物料供应:物料供应员每次都供应单套的物料,不断地在准备区和生产线料架上有节奏地走动.而我们大多一天配4次左右的物料,每次物料配送的数量都很大.
③对一线员工教育的重视:对上岗的一线员工都有一套作业的训练,达到要求后才能上岗.我们直接上岗,大多数都由老员工进行指导,没有完善的培训体系.
……
综合以上,我们可以知道本次日本工厂参观学习之旅,有震撼、有冲击、有对比、有反思,证明大家都用心投入把握住了这次难能可贵的机会.在这之后就是心动不如行动的大舞台,等着我们去挑战现实的局面,以此展现瑞铃的实力!
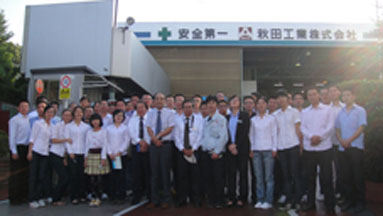